CeO2
precursor was successfully prepared via the One Pot process. On
the basis of mass spectroscopy, the precursor was proposed to be
monometallic species consisting of one TEA group per metal ion or
a monometallic species consisting of one TEA group per metal ion
and a nitrate group. The precursor was converted to CeO2
by sintering at 600, 800, and 1000oC for 2 h in air.
Light yellowish colored powders were studied by XRD.
Introduction : Fuel cells
are expected for a practical power generation and environmental
friendly devices converting the chemical energy directly into electrical
energy under the processes of electrochemical reaction. Solid oxide
fuel cells, based on oxide-ion conducting electrolyte, offer clean,
low-pollution technology to electrochemically generate electricity
at high efficiencies. Up to now, various researches have been focused
on the improvement of the SOFCs performance and stability. Electrolytes
providing high oxide ion conductivity and being operated at low
temperature are developed. Ceria (CeO2) is a fluorite-structured
oxide that can form extensive solid solutions with a variety of
cations while keeping the fluorite crystal structure. Doped ceria
has been considered as one of the most promising electrolyte materials
for intermediate temperature-solid oxide fuel cells. Chemical routes
to ceramics offer many advantages over traditional methods, including
the potential to control product homogeneity and purity, to lower
processing temperatures. One of them called the one pot process,
is very simple and straightforward. It provides high purity and
homogeneity product. Due to the advantage as mentioned above, in
this research work, metal-organic precursor of cerium is prepared
via one pot synthesis.
Methodology: Ce(NO3)3.6H2O
and triethanolamine were reacted in n-propanol for 4 h. The solid
products were characterized by ESI-MS, TGA, and FTIR. The precursor
was sintered in a furnace for 2 h with various temperatures such
as 600, 800 and 1000oC. The powder was characterized
by XRD.
Results and Discussion:
The reactions of Ce(NO3)3.6H2O and TEA were
proceeded in n-proponol to obtain the homogeneous solution. The
yellowish powder was precipitated when the reactants were completed
reacted for 4 h. The FTIR spectrum of precursor showed C-H stretching
bands occurred in the region 2928 and 2890 cm-1 was assigned
for -CH2- group in the product. In addition, the resonance
at 1080 cm-1 was ascribed to the Ce-O-C stretching vibration,
and the band at 550 cm-1 is due to the Ce-O stretching.
The precursor structure was then characterized by using electrospray
ionization (ESI) Mass spectroscopy. Two significant peaks were generated
at m/z = 286 and 348, respectively. However, these two peaks exhibited
in different intensity. The possible structures of product (Figure
1) were proposed to be a monometallic species consisting of one
TEA group per metal ion (Structure I) and a monometallic species
consisting of one TEA group per metal ion and a nitrate group (Structure
II). The appropriate temperature for sintering was studied by TGA.
Two weight loss regions appeared in the TGA thermogram. It was found
that after 800oC, no weight loss was generated; the appropriate
sintered temperatures were therefore varied in the range of 800-1000oC
for preparing CeO2 powder. In addition, the ceramic yield
was found to be 32%. The precursors were pyrolyzed at various temperatures,
such as 600, 800, and 1000oC for 2 h in air. Light yellowish
colored powders were characterized by powder X-ray diffraction (XRD).
Peak positions of all products were identified corresponded to the
fluorite structure by comparing with JCPDS file No. 34-0394. The
XRD patterns of all products were not different in positions as
comparing with the standard XRD pattern
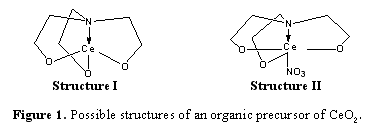
Conclusion: The
One Pot Process was successfully used to prepare the CeO2 powder.
This method also offers an easy, inexpensive, straightforward alternative
to solid-solid reaction, co-precipitation and other chemical techniques
of ceramics processing, and retains the advantages of purity, homogeneity,
and low processing temperatures. The powders will be further studied
in the second stage as following the research plan concerned with
application as an electrolyte membrane for solid oxide fuel cell.
|